Precision CNC Machining for Steel and Wire Industry Components
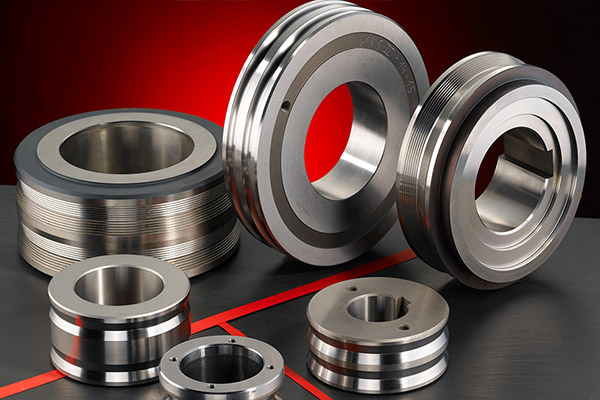
===INTRO:===
The steel and wire industry forms the backbone of modern manufacturing, infrastructure, and transportation. As demands for higher performance, durability, and precision grow, so does the need for ultra-accurate, reliable components. Precision CNC machining has emerged as an essential technology in producing high-quality steel and wire industry parts. Its ability to deliver complex geometries, tight tolerances, and consistent quality makes it a game-changer for manufacturers seeking to optimize performance and reduce waste. This article explores how advanced CNC machining solutions are transforming the production of steel and wire components, addressing industry challenges, material considerations, and showcasing our capabilities and successful client collaborations.
The Growing Demand for Precision CNC Machining in Steel and Wire Components
In today’s competitive landscape, the demand for precision CNC machining in the steel and wire sector is increasing rapidly. Industries such as automotive, aerospace, construction, and electronics require components that meet stringent specifications for strength, flexibility, and longevity. These components often feature complex shapes, micro-holes, and intricate details that traditional manufacturing methods struggle to produce efficiently.
With the evolution of CNC technology, manufacturers can now achieve micron-level tolerances, ensuring parts fit perfectly and function flawlessly. The demand for customized, high-precision parts is driven by industry needs to reduce assembly time and minimize failures caused by manufacturing defects. Furthermore, rapid prototyping and small-batch production are becoming more feasible with CNC machining, allowing companies to innovate faster and respond swiftly to market changes.
As steel and wire components become more integral to advanced machinery and infrastructure projects, the importance of precision in machining cannot be overstated. High-value applications, such as precision springs, connectors, and reinforcement bars, rely heavily on the tight tolerances and surface finishes that CNC machining provides. This trend underscores the industry’s shift toward embracing precision CNC technology as a core manufacturing process.
Another factor fueling this demand is the ongoing push for sustainability and resource efficiency. CNC machining reduces material waste through precise material removal, and its automation capabilities enable continuous, consistent production. As environmental regulations tighten, manufacturers are increasingly turning to CNC solutions to meet both quality standards and eco-friendly manufacturing goals.
The integration of smart CNC systems with IoT (Internet of Things) technology further enhances traceability, quality control, and process optimization. Real-time data collection enables proactive adjustments, minimizing errors and ensuring every component adheres to strict specifications. This interconnected approach aligns with the evolving needs of the steel and wire industry for smarter, leaner production processes.
Ultimately, the rising complexity of steel and wire components combined with the need for high-volume, high-precision production makes CNC machining indispensable. It not only meets current industry standards but also paves the way for innovative solutions and new design possibilities, reinforcing its vital role in the future of steel and wire manufacturing.
Overcoming Manufacturing Challenges with Advanced CNC Machining Solutions
Manufacturing steel and wire components presents unique challenges, from material toughness to precision requirements. Traditional machining methods often struggle with these complexities, leading to longer production cycles, increased costs, and compromised quality. Advanced CNC machining solutions have been developed to address these obstacles effectively.
One primary challenge is machining hard, abrasive steels that resist cutting and generate excessive tool wear. High-performance CNC machines equipped with advanced tools and coatings can handle these materials efficiently, extending tool life and maintaining consistent quality. Multi-axis machining centers enable complex geometries to be produced in fewer setups, reducing errors and production time.
Achieving tight tolerances in large or intricate parts requires precise control over machine movements and environmental stability. Modern CNC systems incorporate advanced feedback sensors, high-precision spindles, and temperature control systems to ensure dimensional accuracy. This precision is critical for components like wire connectors and steel reinforcements, where even minute deviations can lead to failure.
Surface finish quality is another challenge, especially for parts involved in electrical or fluid transfer applications. CNC machining techniques such as fine finishing, polishing, and laser-assisted processes can deliver superior surface quality, minimizing post-processing. This is vital for maintaining conductivity, corrosion resistance, and aesthetic standards.
Material deformation during machining is a common issue with steel components subjected to high cutting forces. Innovative fixturing solutions, vibration damping, and optimized cutting parameters help mitigate these effects, ensuring dimensional stability throughout production.
Automation and CNC programming advancements reduce human error and improve repeatability, essential for high-volume production runs of wire industry parts like springs or precision shafts. Adaptive feed controls and real-time monitoring allow for dynamic adjustments, addressing material inconsistencies or tool wear.
Finally, integrating quality inspection tools such as coordinate measuring machines (CMM) and inline optical scanners with CNC systems ensures each component meets strict specifications. Real-time feedback loops facilitate immediate corrections, reducing scrap and rework. Together, these advanced CNC solutions dramatically enhance manufacturing efficiency, quality, and cost-effectiveness in the steel and wire industry.
Key Materials in Steel and Wire Industry Components and Their Characteristics
Selecting the right material is crucial for CNC machining of steel and wire components, as it directly influences process parameters, tool selection, and final performance. Understanding the characteristics of common materials helps optimize machining strategies and achieve desired quality standards.
Carbon Steel: Widely used due to its strength and affordability, carbon steel offers excellent machinability with proper heat treatment. It is suitable for structural components, fasteners, and springs. Its high hardness post-heat treatment demands robust cutting tools and precise control to prevent deformation.
Alloy Steel: Enhanced with elements like chromium, nickel, or molybdenum, alloy steels provide superior toughness, corrosion resistance, and wear properties. They are ideal for demanding applications such as high-stress machine parts and hydraulic components. Machining these materials requires high-powered CNC machines with appropriate tooling.
Stainless Steel: Known for corrosion resistance and aesthetic appeal, stainless steel is common in medical, food processing, and electrical industries. It is more challenging to machine due to its work-hardening tendencies, necessitating specialized cutting tools and slower feed rates to prevent tool wear and surface imperfections.
High-Speed Steel (HSS) and Carbide: For precision parts, carbide tools are preferred for their hardness and durability, especially when machining hardened steels. HSS tools are economical and suitable for less demanding tasks or softer steels. Their selection impacts surface finish and productivity.
Wire Materials (Spring Steel, Copper, Aluminum): Wire components require materials with specific flexibility and conductivity qualities. Spring steel offers elasticity but is hard to cut, while copper and aluminum are softer and more machinable, suitable for electrical contacts and flexible conductors. Wire diameter and material properties influence tool choice and machining parameters.
Specialty Alloys (Inconel, Titanium): Used in high-performance applications like aerospace, these materials pose significant machining challenges due to their toughness and low thermal conductivity. CNC machining of such materials demands precise temperature management, high-performance tooling, and slow machining feeds.
Surface Treatments and Coatings: Many steel and wire components undergo surface modifications like nitriding, plating, or anodizing to improve hardness, corrosion resistance, or aesthetic qualities. These treatments affect machining strategies, requiring adjustments in cutting parameters and tool selection to preserve surface integrity.
By understanding these materials’ properties, manufacturers can design optimal CNC machining processes that maximize efficiency, minimize tool wear, and produce components that meet rigorous industry standards.
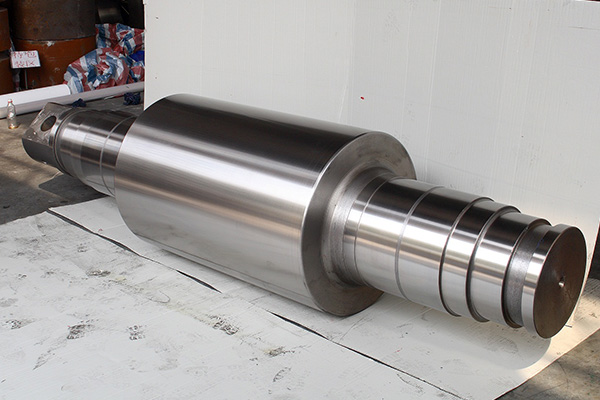
Custom machining of high-precision parts for steel manufacturing and wire forming
Showcasing Our Precision CNC Machining Capabilities and Quality Standards
Our CNC machining facility is equipped with state-of-the-art technology designed specifically for the demanding requirements of steel and wire industry components. We pride ourselves on delivering precision, consistency, and top-tier quality that meet or exceed industry standards.
Our multi-axis CNC machining centers feature high-speed spindles, advanced control systems, and adaptive tool changers, enabling us to produce complex geometries quickly and accurately. These machines are capable of achieving tolerances as tight as ±0.005mm, ensuring perfect fit and function for critical components.
We utilize a comprehensive suite of inspection and measurement tools, including coordinate measuring machines (CMM), laser scanners, and optical comparators, to verify every batch against strict quality specifications. Our in-house quality assurance process guarantees that each part is inspected thoroughly before delivery.
Surface finishing is a key aspect of our capabilities; we provide polishing, grinding, and coating services to enhance surface quality, corrosion resistance, and aesthetic appeal. Our team is experienced in working with various materials, from hardened steels to delicate wire components, ensuring optimal processing conditions for each.
Automation and software integration allow us to streamline production workflows, reduce lead times, and maintain consistency across large batches. Our machining processes are continuously monitored and optimized using real-time data, minimizing defects and maximizing efficiency.
We adhere to international standards such as ISO 9001, ensuring that our quality management systems support consistent, reliable output. Our certifications and adherence to industry best practices demonstrate our commitment to excellence in CNC machining for steel and wire components.
Customer collaboration is central to our approach; we work closely with clients from prototype development through high-volume manufacturing, providing tailored solutions that meet specific technical and commercial requirements. With our advanced capabilities and strict quality standards, we are your trusted partner for precision CNC machining in the steel and wire industry.
Commonly Machined Parts and Their Critical Applications in the Industry
The steel and wire industry relies on a variety of machined parts that play essential roles in their respective applications. Precision machining ensures these components perform reliably under demanding conditions and adhere to strict specifications.
Springs: Coiled or flat springs made from high-tensile wire or steel strips are machined to precise dimensions to provide elasticity in machinery, automotive suspensions, and electronic devices. Their performance depends heavily on tight tolerances and surface finish.
Connectors and Terminals: Copper or steel connectors are crucial for electrical wiring, ensuring secure and conductive connections. CNC machining allows for micro-holes, threads, and complex geometries essential for reliable electrical contacts.
Reinforcement Bars and Meshes: Structural steel components like reinforcing bars are machined or cut to size with high precision to ensure proper fitment in construction. Accurate machining minimizes material waste and enhances structural integrity.
Valves and Fittings: Stainless steel valves, fittings, and adapters are machined for fluid and gas control systems. Their dimensions and surface quality directly impact performance, pressure resistance, and longevity.
Precision Shafts and Pins: Used in automotive transmissions, machinery, and wire drawing equipment, these components require high concentricity and surface quality to ensure smooth operation and longevity.
Wire Forming Parts: Customized wire forms, clips, and brackets are machined for applications in electronics, medical devices, and appliances. Their intricate shapes demand advanced CNC programming and tooling.
Medical and Dental Instruments: Certain steel components are machined with ultra-high precision for medical tools, surgical instruments, and dental devices, demanding impeccable surface finish and tight tolerances.
Aerospace Components: Titanium or specialized steel parts, such as fasteners and structural elements, are machined to exceptional standards for aircraft and spacecraft, where safety and performance are paramount.
These components are vital for industry performance, safety, and durability. Precision CNC machining ensures they meet the rigorous standards required for their critical applications, making it possible to push the boundaries of innovation in the steel and wire sector.
Successful Projects and Client Collaborations in Steel and Wire Components Manufacturing
Our expertise in CNC machining has enabled us to successfully deliver numerous projects for clients across the steel and wire industry. These collaborations highlight our capabilities in handling complex designs, tight tolerances, and high-volume production requirements.
One notable project involved producing high-precision wire forming components for an electronics manufacturer. Utilizing our multi-axis CNC wire bending machines, we manufactured intricate wire clips with micro-holes and precise bends, meeting the tight tolerances specified. The successful delivery enabled the client to improve their assembly efficiency and product reliability.
Another example is a collaboration with a construction steel fabricator, where we machined custom reinforcing bars with specific surface finishes and dimensional standards. Our advanced CNC mills and inspection protocols ensured compliance with structural safety requirements, reducing rework and material waste.
For the aerospace sector, we supplied machined fasteners made from titanium alloys. These components required exceptional surface quality, minimal residual stress, and strict adherence to aerospace standards. Our precise control over machining parameters and surface treatments made this project a success, earning trust from the client for future collaborations.
We also partnered with a medical device company to produce stainless steel surgical instruments. The parts demanded ultra-high precision, corrosion resistance, and impeccable surface finishes. Our ability to deliver consistent quality helped the client meet stringent regulatory standards and streamline their production process.
Our ongoing collaborations involve providing prototype development, small-batch runs, and large-scale production, demonstrating our flexibility and commitment to client satisfaction. Each project is approached with meticulous attention to detail, leveraging our advanced CNC technology and experienced team to ensure optimal results.
Through these successful projects, we have built a reputation for delivering high-quality, reliable, and innovative CNC machining solutions tailored to the specific needs of the steel and wire industry. Our proven track record and dedicated customer support make us the ideal partner to help your business succeed.