Precision CNC Machining Solutions for Aerospace High-Precision Parts
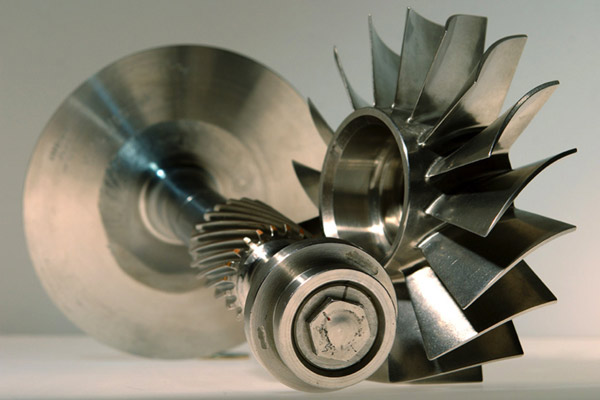
In the rapidly evolving aerospace industry, the demand for high-precision components has never been greater. From intricate engine parts to structural elements, aerospace manufacturers require CNC machining solutions capable of delivering exceptional accuracy, durability, and consistency. As aircraft designs become more complex and performance standards higher, the role of precision CNC machining in producing these critical parts becomes essential. This article explores the key aspects of aerospace high-precision parts manufacturing, highlighting the challenges, materials, capabilities, and real-world applications that define this specialized industry.
The Growing Need for High-Precision Aerospace CNC Machined Parts
The aerospace sector is characterized by its rigorous standards for safety, performance, and reliability. As aircraft designs evolve, components must meet increasingly stringent specifications, often with tolerances measured in microns. High-precision CNC machining offers the impeccable accuracy needed to produce complex geometries that traditional manufacturing methods cannot achieve. The demand for lightweight yet strong parts drives the need for advanced materials and precise fabrication techniques.
Furthermore, the integration of sophisticated systems—such as avionics, propulsion, and structural frameworks—requires components that fit together flawlessly. This necessity pushes aerospace manufacturers to seek CNC machining solutions that can consistently deliver high-precision parts at scale. The growing trend towards automation and smart manufacturing also ensures faster turnaround times and tighter quality controls, which are critical in aerospace production.
In addition, regulatory bodies like FAA and EASA impose strict certification standards for aerospace components. Achieving compliance demands not only advanced manufacturing processes but also rigorous inspection and quality assurance measures. High-precision CNC machining thus becomes a strategic advantage for aerospace companies aiming to maintain competitive edges while meeting regulatory demands.
Another significant factor is the increasing adoption of additive manufacturing combined with CNC machining to create complex assemblies. This hybrid approach necessitates highly precise machining to complement 3D-printed components, further emphasizing the importance of CNC solutions in aerospace production lines.
The aerospace industry’s focus on sustainability and fuel efficiency also influences component design, promoting the use of lightweight materials and innovative structures. CNC machining’s ability to work with a wide range of advanced materials ensures that aerospace manufacturers can realize these design goals effectively.
Moreover, as global aerospace markets expand—with new aircraft programs and aftermarket services—the need for reliable, high-precision manufacturing partners grows. CNC machining firms equipped with the latest technology become critical collaborators in delivering parts that meet demanding specifications and tight schedules.
Lastly, the integration of digital twin technology and real-time monitoring in CNC machining processes enhances precision, traceability, and quality management. These technological advancements contribute to reducing waste and rework, thus lowering costs while maintaining high standards.
In sum, the ever-increasing complexity and safety requirements of aerospace components make high-precision CNC machining indispensable. Manufacturers investing in advanced CNC solutions are better positioned to meet the industry’s evolving demands for precision, quality, and efficiency.
Overcoming Challenges in Precision CNC Machining for Aerospace Components
Manufacturing aerospace high-precision parts via CNC machining is fraught with challenges stemming from material complexities, intricate geometries, and strict quality standards. One primary obstacle is achieving and maintaining tight tolerances over large or complex parts, which requires state-of-the-art equipment and meticulous process control. Variations in temperature, tool wear, and machine calibration can all negatively impact dimensional accuracy, making rigorous monitoring essential.
Another challenge involves working with advanced materials such as titanium alloys, Inconel, and composite composites. These materials offer the strength-to-weight ratio and corrosion resistance necessary for aerospace applications but are notoriously difficult to machine due to their hardness, chip formation tendencies, and thermal properties. Overcoming these issues demands specialized cutting tools, optimized machining parameters, and sometimes, innovative cooling techniques.
Surface finish is also critical in aerospace components, not only for aesthetics but for performance and safety. Achieving a high-quality surface finish often involves multiple machining passes, fine-tuning of cutting parameters, and additional finishing processes like polishing or deburring. Managing these processes efficiently without sacrificing accuracy presents a significant challenge.
The complexity of aerospace parts often leads to lengthy setup times, requiring precise fixturing and programming. Ensuring repeatability across batches is vital, especially for parts that must meet rigorous certification standards. This calls for advanced CAD/CAM software and precise fixture design to reduce setup errors and cycle times.
Material waste and cost control are ongoing concerns, especially when machining exotic or expensive alloys. Through intelligent tool path planning and high-efficiency machining techniques, manufacturers strive to minimize waste while maximizing throughput. Advanced simulation software can predict potential issues before machining begins, saving both time and materials.
The advent of Industry 4.0 technologies—such as real-time process monitoring, predictive maintenance, and data analytics—helps address these challenges by enabling proactive adjustments and quality assurance. These innovations allow CNC machines to operate at optimal conditions, reducing downtime and variability.
Implementing rigorous inspection and quality control protocols, including coordinate measuring machines (CMM) and non-destructive testing, ensures that each part meets aerospace standards. Traceability throughout the manufacturing process is vital for compliance and long-term reliability.
Finally, ongoing workforce training and process standardization are crucial. Skilled operators and engineers understand the nuances of machining difficult aerospace alloys and complex geometries, which ultimately ensures higher yields and better product consistency.
Overcoming these challenges requires a combination of cutting-edge technology, skilled personnel, and rigorous process management. When effectively addressed, they enable the production of aerospace high-precision parts that meet the highest safety and quality standards.
Key Materials Used in Aerospace High-Precision CNC Machining
The selection of materials is fundamental to the performance and longevity of aerospace components. High-strength, lightweight materials are preferred to optimize fuel efficiency and structural integrity. Titanium alloys, such as Ti-6Al-4V, are renowned for their excellent strength-to-weight ratio, corrosion resistance, and biocompatibility, making them ideal for engine components, airframe structures, and fasteners. However, their machinability poses unique challenges, necessitating specialized tooling and process control.
Inconel alloys, particularly Inconel 718, are nickel-based superalloys that withstand extreme temperatures and oxidizing environments. These materials are essential for turbine blades, exhaust systems, and hot-section components. Their high hardness and thermal stability demand advanced cutting techniques and cooling methods to achieve precision without inducing micro-cracks or distortions.
Aluminum alloys, such as 7075 and 2024, offer a lightweight yet strong alternative for various aerospace parts. They are easier to machine and cost-effective, making them suitable for structural panels, interior parts, and control surfaces. Their high thermal conductivity also benefits rapid heat dissipation during machining.
Composites like carbon fiber reinforced polymers (CFRPs) are increasingly used due to their lightweight and high-strength properties. Machining CFRPs requires specialized tools to prevent delamination and fiber pullout. CNC machining of composites often involves lower cutting speeds and optimized tool paths to preserve material integrity.
Magnesium alloys, such as AZ91D, provide another lightweight option for certain aerospace applications. Their excellent strength-to-weight ratio makes them suitable for interior components and housings, although their flammability and corrosion susceptibility must be carefully managed.
Ceramic materials, though less common, are employed for specialized high-temperature applications like thermal protection systems. Machining ceramics requires diamond-coated tools and precise control due to their brittleness.
The choice of material also depends on factors like load conditions, environmental exposure, and manufacturing cost. Ensuring compatibility between material properties and CNC machining parameters is crucial for producing reliable aerospace parts.
In addition to raw material selection, surface treatments such as anodizing, passivation, or coating are applied to enhance corrosion resistance and wear properties. These processes integrate seamlessly with CNC manufacturing to deliver parts that meet aerospace industry standards.
Overall, the diverse range of materials used in aerospace high-precision CNC machining reflects the industry’s need for innovative solutions that balance strength, weight, and durability. Mastery over machining techniques across these materials is essential for producing components that perform reliably in demanding environments.
Showcasing Our Capabilities: Tolerances, Equipment, and Quality Control
Our state-of-the-art CNC machining facilities are equipped to meet the highest standards of precision and quality for aerospace high-precision parts. We consistently achieve tolerances as tight as ±0.005 mm (±5 microns), ensuring each component fits perfectly within complex assemblies. This level of accuracy is critical for aerospace applications where even minor deviations can compromise safety or performance.
Our equipment portfolio includes multi-axis CNC milling centers, high-precision lathes, and 5-axis machining centers capable of handling complex geometries in a single setup. These machines are fitted with the latest control systems that enable precise tool movement and repeatability. The use of high-speed spindles, rigid fixtures, and advanced tooling allows us to optimize cutting conditions for different materials and part complexities.
We utilize advanced CAD/CAM software to simulate machining processes pre-production, reducing errors and cycle times. This digital approach ensures that tooling paths are optimized for material removal rates, surface finish, and dimensional accuracy. Automated tool changers and adaptive machining techniques further enhance efficiency and consistency.
Quality control is embedded at every stage of production. Our facilities are equipped with coordinate measuring machines (CMMs), laser scanners, and non-destructive testing (NDT) methods to verify dimensions and detect defects. All parts undergo rigorous inspection before delivery, with documentation available for traceability and certification purposes.
We adhere to international standards such as AS9100 and ISO 9001, which underpin our commitment to quality, safety, and continuous improvement. Our certified inspection processes align with aerospace industry requirements, ensuring parts meet or exceed regulatory specifications.
Process standardization allows us to maintain high repeatability across large production runs. Our skilled engineers and technicians continuously monitor machining parameters, adjust for tool wear, and implement preventive maintenance to prevent deviations and downtime.
Incorporating Industry 4.0 technologies, we implement real-time data analytics and machine monitoring systems that provide insights into process stability. This proactive approach minimizes scrap rates and enhances overall production efficiency.
Ultimately, our comprehensive capabilities ensure that every aerospace high-precision CNC machined part we produce is of the highest quality, meeting all dimensional and surface finish specifications, and ready for rigorous aerospace applications.
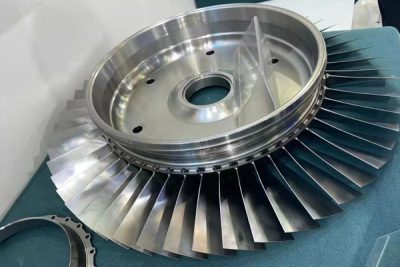
Customized machining of high-precision aerospace components
Common Aerospace Parts Manufactured via CNC Machining and Their Applications
CNC machining plays a pivotal role in manufacturing a wide array of aerospace components, each vital to the safety and efficiency of aircraft. Engine components such as turbine blades, compressor disks, and fuel nozzles are fabricated with extreme precision to withstand high temperatures and mechanical stresses. These parts are often made from superalloys like Inconel and titanium alloys to ensure durability.
Structural components, including fuselage frames, wing spars, and internal support brackets, benefit from CNC’s ability to produce complex, lightweight geometries. Aluminum and composite materials are typical choices, optimized through precise machining to reduce weight without compromising strength.
Landing gear components, such as shock absorbers, struts, and axles, demand high load-bearing capacity and corrosion resistance. CNC machining enables the production of these parts with tight tolerances to ensure smooth operation and safety during takeoff and landing cycles.
Avionics housings, connectors, and panels are manufactured with high precision to fit seamlessly within electronic systems. CNC machining ensures accurate threading, fine surface finishes, and complex geometries necessary for integration with other aircraft systems.
Interior cabin components, including seat frames, lighting fixtures, and control panels, benefit from CNC machining’s ability to produce intricate designs with excellent surface quality. These parts must meet both aesthetic and functional standards.
Fuel and hydraulic system components, such as valves, pumps, and piping fittings, require precision fabrication to prevent leaks and ensure reliable operation under extreme conditions. CNC machining’s versatility allows for the production of these critical parts across various materials.
Emergency and safety equipment components, like fire extinguisher mounts and escape system brackets, also rely on CNC fabrication for their precision and resistance to harsh environments.
Maintenance and aftermarket parts, including replacement engine parts and structural repairs, are often produced via CNC machining to meet original specifications, ensuring longevity and compatibility.
Overall, CNC machining’s flexibility and precision make it indispensable across all segments of aerospace manufacturing, enabling the production of parts that meet rigorous safety, performance, and durability standards.
Real-World Success Stories in Aerospace High-Precision Part Manufacturing
Our commitment to excellence is demonstrated through numerous successful collaborations with leading aerospace manufacturers worldwide. One notable project involved the production of titanium engine components for a major commercial aircraft program. Using advanced 5-axis CNC machining, we achieved tolerances within ±0.005 mm, ensuring perfect fit and performance in high-temperature environments. The project required meticulous process control and extensive inspection, ultimately resulting in a reliable component delivered on time to meet tight production schedules.
Another success story highlights the manufacturing of high-strength aluminum structural parts for unmanned aerial vehicles (UAVs). Through optimized tool paths and high-speed machining, we reduced cycle times by 30% while maintaining strict quality standards. This efficiency enabled the client to accelerate their production timeline and improve overall cost-effectiveness.
We also partnered with a leading aerospace supplier to produce complex composite brackets, employing CNC machining combined with precise tooling adjustments to prevent delamination and fiber pullout. The result was lightweight, durable parts that contributed to the overall fuel efficiency of the aircraft.
A recent project involved the fabrication of Inconel fuel nozzles for a commercial jet engine. The parts required intricate internal passages and ultra-fine surface finishes. Our advanced process monitoring and quality assurance protocols ensured each part met OEM specifications, passing all certification tests.
Furthermore, our team successfully delivered customized maintenance spare parts for legacy aircraft fleets, adhering to original manufacturer specifications. This not only extended the service life of these aircraft but also demonstrated our ability to deliver precision parts under tight deadlines.
These real-world examples underscore our expertise and dedication to providing aerospace high-precision CNC machining solutions that meet and exceed industry standards. Our track record of successful projects highlights our capacity to handle complex geometries, challenging materials, and demanding quality requirements.
If you’re seeking a reliable partner for your aerospace component manufacturing needs, contact us today to discuss how our precision CNC machining solutions can bring your projects to life with unmatched quality and efficiency.
In the high-stakes world of aerospace engineering, precision and reliability are paramount. Through advanced CNC machining solutions, we enable manufacturers to produce complex, high-performance parts that meet the industry’s toughest standards. From selecting the right materials to leveraging cutting-edge equipment and rigorous quality control, our expertise ensures every component performs flawlessly in demanding environments. Partner with us for your aerospace high-precision parts manufacturing needs, and experience the difference that precision, innovation, and commitment can make. Reach out today for a customized quote and discover how we can support your aerospace success.