Precision CNC Machining Solutions for High-Precision Semiconductor Components
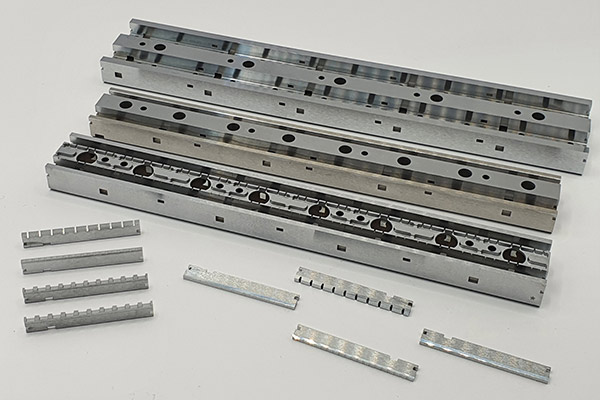
The semiconductor industry is at the forefront of technological innovation, powering everything from smartphones and computers to advanced medical devices and aerospace systems. As devices become more compact and functionally complex, the demand for high-precision semiconductor components has surged. Achieving the exacting tolerances required for these tiny yet crucial parts demands expertise, sophisticated equipment, and meticulous quality control. Precision CNC machining solutions have become indispensable in meeting these stringent standards, enabling manufacturers to produce reliable, high-performance semiconductor components with unmatched accuracy. In this article, we explore the vital role of advanced CNC machining in the high-precision semiconductor sector, highlighting challenges, materials, capabilities, and how partnering with experienced providers can elevate your project success.===
The Growing Demand for Precision in Semiconductor Component Manufacturing
The semiconductor industry’s rapid growth stems from the increasing miniaturization and complexity of electronic devices. As devices shrink, the components inside must also meet tighter dimensional tolerances, often within micrometer or even sub-micrometer ranges. High-precision semiconductor components such as microfluidic channels, thin wafers, and intricate connectors require manufacturing processes capable of delivering exceptional accuracy and consistency.
This heightened demand for precision is driven by several factors. First, the push for faster data processing and energy efficiency necessitates smaller, more efficient components. Second, the integration of multiple functionalities into a single chip has increased complexity, demanding parts with extremely tight tolerances. Third, the need for high reliability and longevity in semiconductor devices makes defect-free, precisely machined parts non-negotiable.
Furthermore, as industry standards evolve, manufacturing firms must adopt more sophisticated technology to stay competitive. This includes CNC machining systems capable of micron-level precision, automation for repeatability, and advanced measurement techniques for quality assurance. The ability to produce high-precision semiconductor components consistently is now a key differentiator for manufacturers aiming to lead in this dynamic market.
Lastly, the global semiconductor supply chain emphasizes quality and speed. OEMs and device manufacturers seek suppliers who can deliver complex parts on time, with impeccable dimensional accuracy. This trend underscores the importance of precision CNC machining solutions tailored for the high-demand semiconductor environment, where even the smallest deviation can lead to significant failures or costly reworks.
Overcoming Challenges in CNC Machining for High-Precision Semiconductors
Manufacturing high-precision semiconductor components via CNC machining presents unique challenges. The first hurdle is the demand for ultra-fine tolerances—often within a few micrometers—which requires highly stable and precise equipment. Variations in tool wear, machine vibrations, and thermal expansion can all compromise accuracy if not properly managed.
Material selection poses another challenge. Semiconductors often involve advanced materials like silicon, sapphire, or specialized alloys, each with distinct machining characteristics. Cutting and shaping these materials without inducing cracks, deformations, or residual stress requires specialized tooling and process parameters.
Achieving complex geometries within strict tolerances also demands multi-axis CNC machines equipped with high-precision spindles and advanced control systems. Such equipment allows for intricate milling, drilling, and cutting operations that are essential for producing micro-scale features. Ensuring process stability over long production runs is critical to maintaining quality consistency.
Contamination control is yet another hurdle. Semiconductor components must be free of particulates and residues, which means cleanroom-compatible machining environments and meticulous handling procedures. This often involves integrating CNC solutions with cleanroom protocols and rigorous filtration systems.
To address these challenges, industry-leading CNC machining providers invest in state-of-the-art equipment, continuous training for operators, and comprehensive quality control systems. These include in-process measurement and inspection technologies such as laser scanners and coordinate measuring machines (CMMs) to verify tolerances in real-time.
Finally, integrating automation and monitoring systems helps mitigate human error and enables rapid adjustments during manufacturing. This proactive approach ensures that high-precision semiconductor parts meet exact specifications consistently, reducing scrap rates and enhancing overall yield.
Key Materials Used in High-Precision Semiconductor CNC Machining
The success of CNC machining for semiconductor components largely depends on selecting the right materials, each offering specific properties suited to different applications. Here are some of the most common materials used:
Silicon: The primary material for semiconductor wafers, silicon boasts excellent electrical properties, thermal stability, and ease of processing. While not typically machined into final components, silicon substrates are often closely integrated with machined parts for microfabrication applications.
Sapphire: Known for its exceptional hardness and optical transparency, sapphire is used in LED substrates, laser windows, and optical components within semiconductor devices. Machining sapphire requires diamond tools and precise control to prevent cracking.
Aluminum and Copper Alloys: These are often used for heat sinks, electronic enclosures, and electrical connectors. Their excellent thermal and electrical conductivities make them vital in thermal management and electrical integration.
Titanium and Specialty Alloys: Used for parts requiring high strength-to-weight ratios, corrosion resistance, and durability. In semiconductor manufacturing, these alloys are employed in vacuum chambers and precision fixtures.
Advanced Ceramics: Materials such as aluminum oxide (Al2O3) and zirconia are utilized for insulating components, microfluidic devices, and wear-resistant parts within semiconductor equipment.
Graphite and Carbon-Based Materials: Due to their thermal stability and machinability, these materials are used for specialized structural components and thermal management parts.
Each material presents unique machining challenges; therefore, selecting the appropriate cutting tools, coolant systems, and process parameters is critical. For example, diamond-tipped tools are essential for hard materials like sapphire, while precision coolant and vibration control are vital when machining brittle ceramics. Understanding the properties of these materials ensures that CNC processes are optimized for quality, efficiency, and durability.
Showcasing Our Capabilities: Tolerance, Equipment, and Quality Control
Our precision CNC machining solutions are designed to meet the rigorous standards of the semiconductor industry. We specialize in delivering components with tolerances as tight as ±2 micrometers, ensuring reliable performance for even the most demanding applications.
We operate a fleet of advanced multi-axis CNC machines, including five-axis milling centers, ultra-precision grinders, and laser micromachining systems. These machines are equipped with high-stability spindles, linear encoders, and real-time feedback control, enabling us to produce intricate features with exceptional accuracy.
Our facility incorporates state-of-the-art measurement and inspection tools, such as coordinate measuring machines (CMMs), laser scanners, and optical comparators. These enable us to perform in-process and final inspections, verifying that each component meets specified dimensions and surface finishes.
Automation plays a vital role in maintaining consistency and reducing human error. We utilize robotic loading and unloading systems, coupled with software-driven process monitoring, to ensure high repeatability and throughput. This integration supports large-volume production without sacrificing precision.
Quality control is embedded throughout our manufacturing process. Our teams follow strict protocols aligned with industry standards like ISO 9001 and IPC standards for electronics manufacturing. Regular calibration and maintenance of equipment guarantee ongoing accuracy.
We also employ statistical process control (SPC) and traceability systems to monitor production metrics closely. When necessary, we provide comprehensive documentation and certificates of conformity to support regulatory compliance and quality assurance.
By combining cutting-edge equipment, rigorous inspection, and a quality-centric approach, we ensure that every high-precision semiconductor component leaving our facility meets or exceeds client expectations, reducing rework and enhancing product reliability.
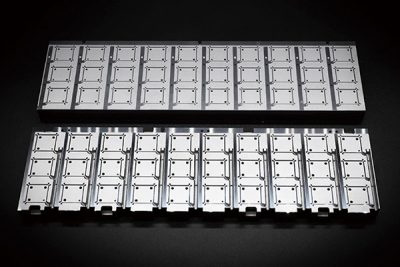
Customized processing of high-precision parts in the semiconductor field
Common Semiconductor Components Manufactured by CNC Machining and Their Uses
CNC machining enables the fabrication of a wide range of semiconductor components, each critical to device performance. Some of the most common parts include:
Microfluidic Channels: Precisely machined microchannels are used in lab-on-a-chip devices, enabling fluid handling at microscopic scales for biological or chemical analysis. Their dimensions and surface qualities are critical for fluid flow control.
Electrical Connectors and Contacts: Custom machined connectors ensure reliable electrical connections within semiconductor modules. Tolerances are vital for maintaining signal integrity and minimizing resistance.
Heat Sinks and Thermal Management Components: High-conductivity metal parts facilitate heat dissipation from sensitive chips, preventing overheating and ensuring stable operation.
Vacuum Chamber Components: Parts made from titanium, aluminum, or ceramics are used in vacuum environments, requiring tight tolerances to maintain vacuum integrity and prevent leaks.
Optical Windows and Lenses: Machined sapphire and quartz components are used for laser and optical applications within semiconductor equipment, demanding surface smoothness and precise dimensions.
Micro-electromechanical Systems (MEMS) Parts: Tiny mechanical components such as resonators, actuators, or sensors are fabricated with CNC precision to meet the exact specifications necessary for functionality.
Each component plays a vital role in the overall semiconductor device, impacting performance, reliability, and longevity. The ability to produce these parts with precision ensures seamless integration, minimal failure rates, and optimized device operation.
Partnering with Experts for Your Semiconductor Precision Machining Projects
Choosing a reliable partner for high-precision CNC machining in the semiconductor industry is crucial to project success. Experienced manufacturers bring not only advanced equipment but also industry knowledge, technical expertise, and a commitment to quality.
A trusted partner offers tailored solutions, from material selection and process development to prototyping and mass production. They understand the nuances of semiconductor manufacturing standards and can provide guidance on design for manufacturability (DFM), helping you optimize your component designs.
Collaboration with industry leaders ensures access to cutting-edge CNC technologies, such as ultra-precision machining, laser micromachining, and cleanroom-compatible processes. These capabilities are essential for achieving the tight tolerances and surface finishes demanded by semiconductor applications.
Furthermore, a dedicated partner emphasizes quality assurance, incorporating in-process inspection, environmental controls, and comprehensive documentation. This reduces risks, shortens lead times, and enhances overall product reliability.
Many top-tier CNC machining providers also offer value-added services such as assembly, surface finishing, and custom packaging, streamlining your supply chain. Their experience in managing complex projects ensures that your high-precision semiconductor components are delivered on time, within budget, and to exact specifications.
By partnering with specialists who understand your industry’s demands, you can focus on innovation and market expansion while leaving the precision machining to experts committed to quality and excellence.
In the fast-evolving semiconductor industry, high-precision CNC machining is the backbone of reliable, efficient, and innovative component manufacturing. From overcoming technical challenges to selecting the right materials and leveraging state-of-the-art equipment, partnering with experienced machining providers can significantly elevate your production capabilities. With meticulous quality control and tailored solutions, we’re here to support your journey toward manufacturing excellence. Contact us today to discuss your high-precision semiconductor machining projects and discover how our expertise can help turn your vision into reality.