Tooling and Mold Machining Expert in CNC Machining
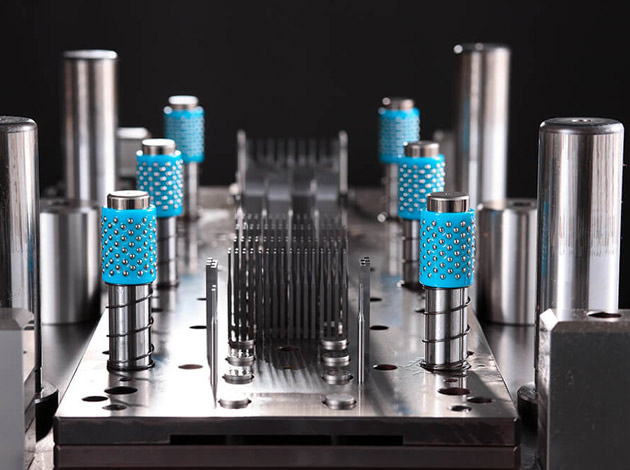
Precision Requirements in the Tooling and Mold Industry
The global manufacturing landscape relies heavily on high-performance tooling and precision molds to enable mass production with consistency, efficiency, and tight tolerances. Whether for injection molding, die casting, stamping, or extrusion, the quality of the mold or die directly influences the reliability, surface finish, and dimensional accuracy of the final product.
To meet the growing complexity of product designs and shorter lead times, mold and tool manufacturers require a trusted tooling and mold machining expert with advanced CNC machining capabilities. This combination of precision engineering and digital manufacturing ensures high-accuracy components that deliver exceptional mold life and production consistency.
Manufacturing Challenges and Technical Solutions
Tooling and mold components are some of the most demanding parts to produce due to:
- Complex 3D geometries, including deep cavities, undercuts, and conformal cooling channels;
- Extremely tight dimensional tolerances for mating surfaces and inserts;
- High hardness materials, often heat-treated before or after machining;
- Surface finish requirements for mirror-like polishing in optical-grade molds;
- Thermal stability and wear resistance to withstand continuous production under heat and pressure.
We address these challenges through:
- 5-axis high-speed CNC milling for intricate mold core and cavity geometries;
- EDM (Electrical Discharge Machining) for sharp internal features, deep ribs, and hardened steel processing;
- CNC grinding for flatness and precision surface control;
- Advanced CAD/CAM programming to ensure optimized tool paths and minimum machining time;
- Polishing, heat treatment, and PVD surface coating for improved mold life and part ejection performance.
Each mold component is processed with strict dimensional control and is customized to your tooling standards, be it DME, HASCO, or proprietary systems.

Commonly Used Materials and Their Properties
Material selection is a critical factor in mold and die manufacturing. We offer machining for a wide range of tool steels and engineering alloys, tailored to specific tooling needs:
- P20 (1.2311 / 1.2312 Tool Steel): Pre-hardened mold steel with good polishability and machinability; ideal for plastic injection molds.
- H13 / SKD61: Hot work tool steel used for die casting and high-temperature molds due to its excellent toughness and thermal fatigue resistance.
- S136 / 420 Stainless Steel: Corrosion-resistant mold steel suitable for medical and food-grade molds.
- 1.2738 / 718H: Pre-hardened alloy with high core hardness and excellent weldability.
- Graphite & Copper Electrodes: For EDM mold manufacturing, offering high wear resistance and fine detail replication.
These materials can be heat-treated to required hardness (up to HRC 52–58), and are selected based on the molding material, production volume, and surface finish needs.
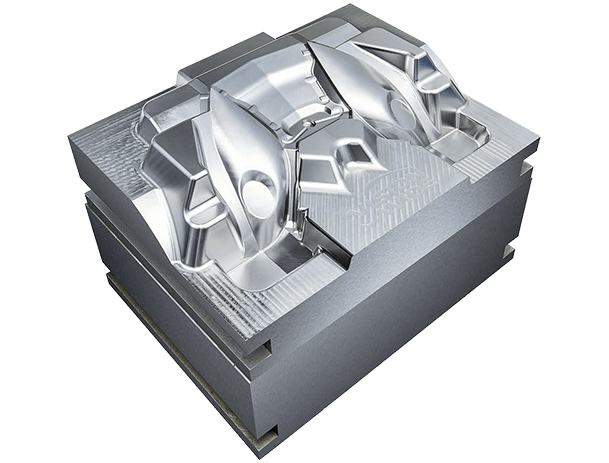
Advanced CNC Machining Capabilities
As a tooling and mold machining expert, we maintain full in-house capabilities to deliver mold bases, inserts, sliders, lifters, cooling systems, and electrodes with unmatched precision.
Machining Highlights:
- Milling: 3-, 4-, and 5-axis CNC machining centers with spindle speeds up to 30,000 RPM
- EDM/WEDM: For hard-to-reach features, ultra-precise cavity and corner formation
- CNC Grinding: Surface grinding and jig grinding for mold base flatness and insert alignment
- Polishing: Mirror polishing, EDM finish control, and texture preparation per VDI or SPI standards
- Tolerances: General ±0.01 mm; critical inserts and cores ±0.003 mm
- Surface Finish: Ra ≤ 0.2 μm for polished surfaces; up to Ra ≤ 0.05 μm with hand lapping
Inspection & Documentation:
- Full CMM reports for dimensional validation;
- Hardness testing, heat treatment charts, and mold material traceability;
- Tool trial tracking or sample part verification if required.
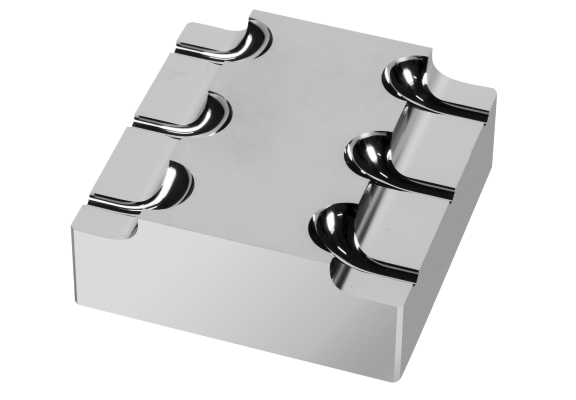
Typical Mold Components and Applications
Our CNC machining services support complete mold tooling and spare parts across industries:
- Plastic Injection Molds: Mold cores and cavities, inserts, lifters, ejector sleeves, hot-runner plates
- Die Casting Dies: Core pins, water jackets, cooling sleeves, gate inserts
- Stamping Dies: Upper and lower die blocks, stripper plates, guide pins
- Medical Tooling: High-polish transparent mold cavities, microfluidic tooling, disposable part molds
- Consumer & Packaging Molds: Multi-cavity injection molds, unscrewing molds, slide actions
Whether you’re building a new mold, revising an existing tool, or sourcing replacement components for high-volume production, our experienced team supports your precision tooling requirements from design to final delivery.
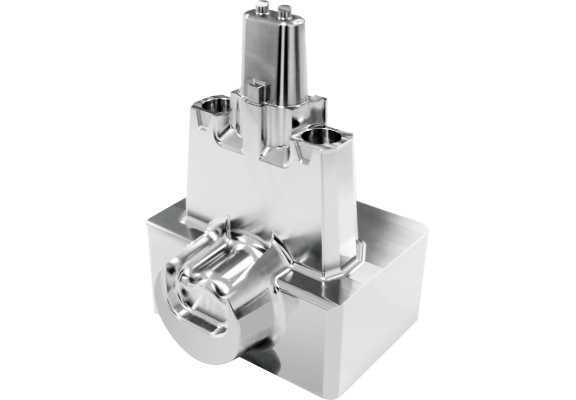
Project Example: High-Cavitation Mold Insert for Medical Parts
For a client in the medical sector, we recently delivered a 16-cavity mold insert set with ultra-tight tolerances:
- Material: S136 stainless steel, hardened to HRC 48
- Cavity Tolerance: ±0.005 mm
- Surface Finish: Ra ≤ 0.1 μm, mirror polished
- Features: Micro channel venting, ejector pin holes, gate land with EDM precision
- Delivery Time: 12 business days from design approval
The tool passed the first-shot qualification and was installed in a 24/7 cleanroom production line.
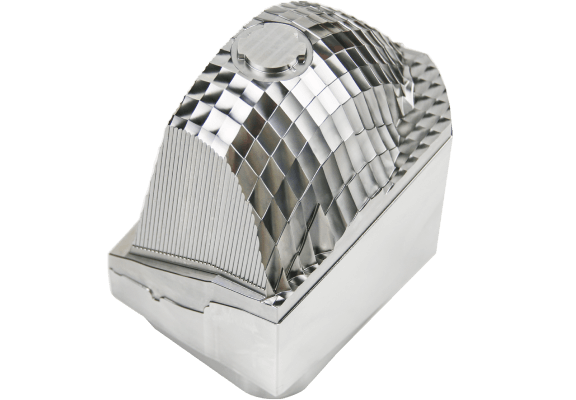
Your Trusted Partner in Tooling and CNC Precision Machining
If your project requires complex mold components, tight-tolerance inserts, or rapid turnaround for spare tooling, we’re here to help. As a tooling and mold machining expert with full CNC machining capabilities, we deliver precision, consistency, and performance—component by component, mold by mold.
👉 Request a Quote Today — Precision Mold Components Engineered for Production Success.
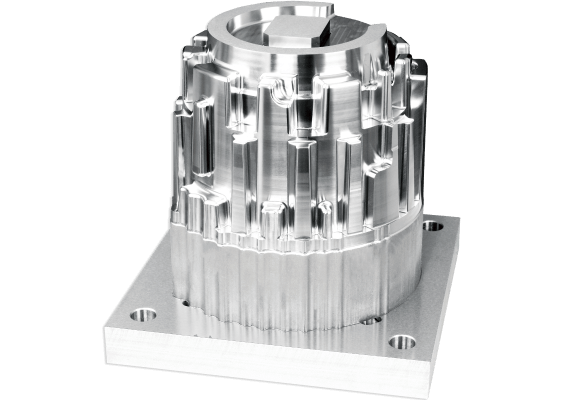