Ultra-Precision Machining of Ceramic Components for the Medical Device Industry
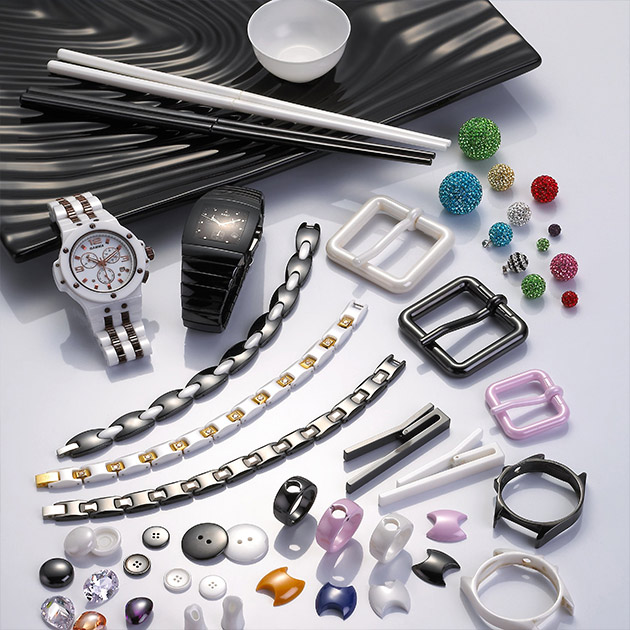
Dimensional tolerances ±0.001mm | Geometric control within 0.002mm
As medical technologies evolve toward miniaturization, biocompatibility, and long-term reliability, technical ceramics have become a material of choice for critical components in surgical tools, implantable systems, and high-performance diagnostic devices. With over 20 years of machining experience, we specialize in custom precision ceramic parts tailored to the demanding standards of the global medical device industry.
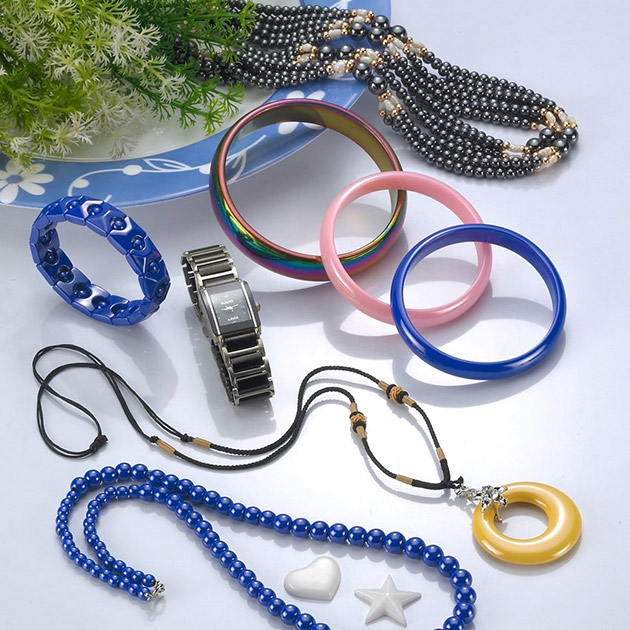
Why Technical Ceramics in Medical Devices?
Ceramic materials such as zirconia, alumina, and silicon nitride offer:
- Exceptional biocompatibility
- Corrosion and chemical resistance
- High wear resistance and hardness
- Radiolucency for imaging applications
- Electrical insulation in implantable electronics
These properties make ceramics ideal for applications ranging from orthopedic implants to surgical instrumentation and fluidic systems in analytical devices.
Equipment & Tolerance Capabilities
Our state-of-the-art facility is equipped with:
- 5-axis high-speed CNC centers for complex geometries
- Swiss-type grinding and polishing systems for submicron finishes
- Tokyo Seimitsu roundness testers and Zeiss CMMs for micron-level inspection
- Cleanroom-compatible cleaning and packaging systems
We consistently achieve:
- ±0.001mm dimensional tolerances
- Geometric tolerances within 0.002mm
- Surface roughness as low as Ra 0.02μm, ensuring tissue compatibility and aseptic integrity
Custom-Made to Your Drawings
Every ceramic component is custom-machined according to customer drawings (CAD/CAM), with our engineering team supporting you from:
- Early design feasibility and DFM reviews
- Material selection based on clinical application
- Custom tooling design to prevent chipping or stress cracking
- Batch traceability and full inspection documentation for FDA/CE compliance
We support both prototype and volume production, with fast lead times and consistent quality across batches.
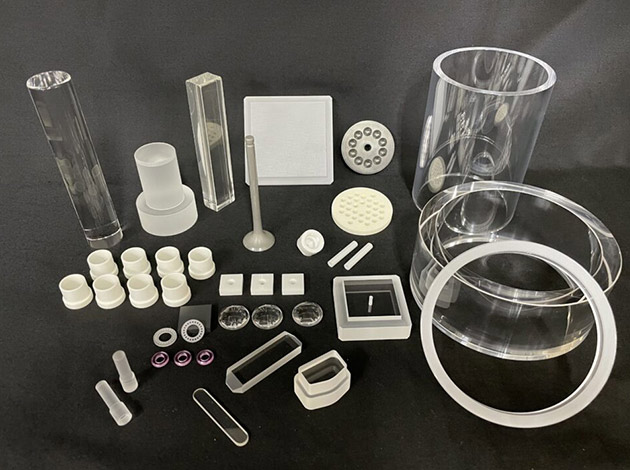
Typical Ceramic Medical Components We Manufacture
- Zirconia dental burs & abutments
- Ceramic surgical scalpel blades
- Bioinert implant heads and cups
- High-precision valve seats & plungers for infusion systems
- Electrical insulators for implantable devices
- Ceramic capillaries and fluidic nozzles for diagnostic tools
Expertise Backed by Global Trust
With more than two decades of ceramic processing know-how, we’ve collaborated with leading OEMs and contract manufacturers across Europe, North America, and Japan. Our ceramic parts are now integrated into medical devices used in cardiology, orthopedics, neurology, dentistry, and minimally invasive surgery.
Quality Beyond Tolerance
Every step of the process—from green body inspection, to finish grinding, to surface cleaning—is optimized for medical-grade reliability. We comply with ISO9001 and support documentation required for Class II & Class III device manufacturing.
Looking for a trusted partner in ceramic precision machining for medical applications?
Let our expertise, equipment, and engineering team bring your product to life—with sub-micron precision and medical-grade integrity.